Case Studies
AI powered continuous vibration monitoring at a Silica factory in Iceland
A fume extraction fan used in a large silica arc furnace plays a crucial role in maintaining a safe and efficient working environment. The proper maintenance of this equipment is of utmost importance, as any failure can result in costly shutdowns.
Challenge
A loose steel plate from the intake duct fell into the fan impeller, causing it to become unbalanced and loose.
Solution
Following this incident, we received a notification about a change in mode with increasing energy levels from the Viking software. Upon a thorough review by our specialists, the issue was detected and diagnosed.
Criticality and Early Anomaly Detection
“Given its critical role in environmental protection and the potential impact on worker safety, early and reliable detection of potential failures in the gas fan is paramount. This goes beyond relying solely on manual inspections or basic alarms.”
Challenge
Undetected Imbalance; A potential imbalance in the fan’s horizontal direction, with 1x being the dominant factor, went unnoticed during traditional monitoring. This imbalance could have resulted in increased vibration, reduced efficiency, and eventual fan failure.
Solution
Proactive Monitoring with AI; The implementation of Viking AI software provided an invaluable solution. By enabling early detection of deviations in the fan’s performance, specifically the rise in velocity at 1x, the AI facilitated proactive monitoring and identification of a potential imbalance.
This early warning system allowed for the fan to be addressed during scheduled maintenance, preventing unplanned downtime and environmental harm.
Preventing Environmental Incidents: Early Detection of Gas Fan Anomalies:
“The gas fan at a facility in Laja, Chile plays a vital role in environmental protection and worker safety. By burning gases, it prevents their release into the atmosphere. However, its effectiveness relies heavily on continuous monitoring to ensure timely detection of potential issues.”
Challenge
Unidentified Imbalance; An imbalance was detected along the main axis of rotation (dominant at 1x frequency). This could have resulted in increased vibration, reduced efficiency, and ultimately, fan failure.
Solution
Advanced wireless vibration sensors enable continuous, high-resolution monitoring (up to 16,000 lines) with customizable frequencies, while offering early detection of equipment issues and fast installation (under an hour). Combined with Viking AI software’s early warnings and predictive maintenance capabilities, this solution prevents downtime and environmental hazards.
Early anomaly detection motor of starch dryer fan
“Given its criticality and the fact that four additional dryers utilize the same type of motor, the early and reliable detection of potential failures is paramount. This goes beyond relying solely on vibration level thresholds set by the vibration analyst.”
Challenge
A shift in the vibration parameter behavior alerted us to an anomaly.
Solution
Upon examining the Mode Change in Viking Analytics software, the vibration analyst could diagnose motor looseness.
Early bearing damaged detection on a large centrifuge
“Not only is the centrifuge vital for our production, but replacing the main bearing is a labor-intensive task spanning 36 hours, carefully planned and scheduled. Failure to adhere to this framework could result in weeks of downtime before the dryer can be operational once more.”
Challenge
Making early detection of any faults in the main bearing.
Solution
A potential bearing failure was identified using the Fast Fourier Transform (FFT) analysis performed by Viking Analytics Algorithms.
Early detection of gearbox failure
Based on historic vibration data collected by sensors in a gearbox shaft, MultiViz Vibration detected asset failure two months before it happened. Automatic Mode Identification found a new operational mode in the equipment, caused by inner raceway failure in the high-speed shaft bearing, which ultimately led to the replacement of the entire gearbox.
Challenge
Early detection of asset failure based on data collected from vibration sensors.
Solution
Automatic Mode Identification found a new operational mode in the equipment, caused by inner raceway failure in the high-speed shaft bearing.
Atypical asset detection in a windfarm
Based on vibration data collected by sensors in bearings, MultiViz Vibration identified the two most atypical wind turbines in a wind farm. The behavior was caused by electrical problems with sensor installation and a major failure that ultimately led to the replacement of an entire gearbox.
Challenge
Discovering which machines need to be prioritized for maintenance in a pool of assets.
Solution
Based on vibration data collected by sensors in bearings, MultiViz Vibration identified the two most atypical wind turbines in a wind farm.
Vibration monitoring of rotating machinery in ships
Based on vibration data collected in a group of fans in a ship, MultiViz Vibration detected the ones that should be prioritized for inspection. Being able to properly monitor machine health allows for better maintenance scheduling to reduce unnecessary interventions in the machines, prevent accidents and increase the resting time of the vessel’s crew.
Challenge
Discovering which machines need to be prioritized for maintenance in a ship, considering the challenges with data transmission and synchronization at sea.
Solution
Based on vibration data collected by sensors in a group of fans, MultiViz Vibration provided a list of assets that had the most atypical behavior.
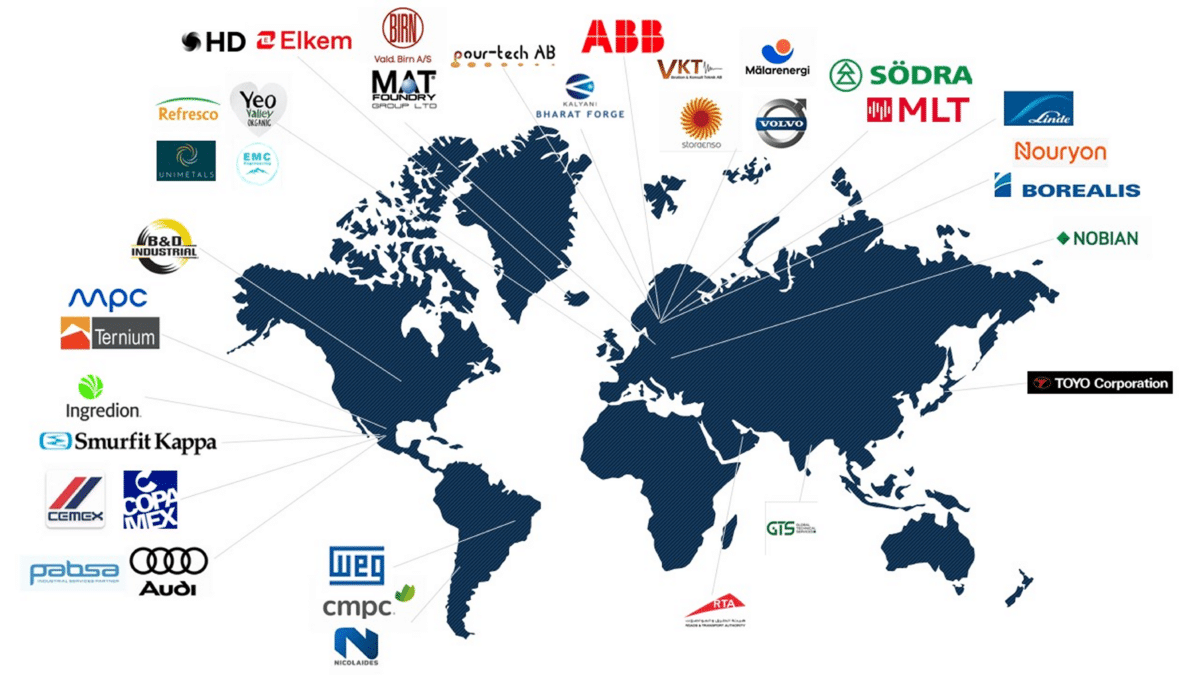